We use cookies to give you the best possible experience. To accept cookies continue browsing, or view our Cookies Policy to find out more.
Easy Guide to Cotton - From the Field to Your Door
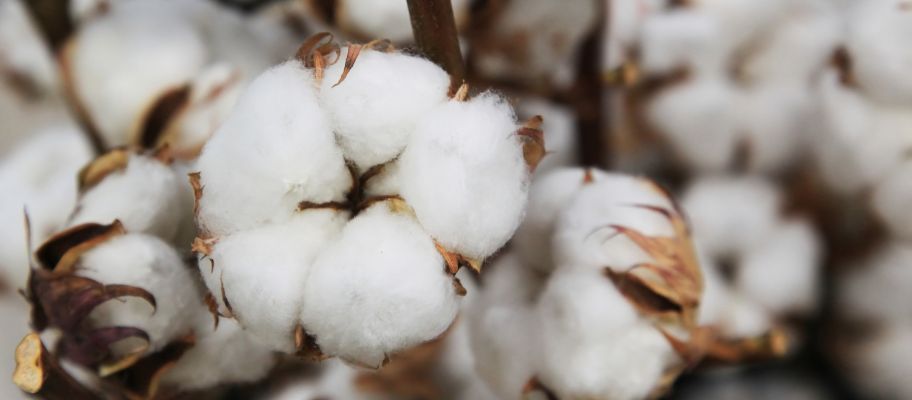
In an industry where comfort, quality, and sustainability are paramount, understanding the journey of cotton from its origins in the field to its final destination can significantly enhance your accomodation’s service offerings. As a leading textile supply company, we are committed to providing you with not only premium products but also valuable insights into the lifecycle of cotton. This guide will walk you through the intricate processes involved in cotton production. Join us as we explore the fascinating world of cotton.
Growing
From planting it takes cotton around three months to flower, with their petals changing from cream to yellow, then pink to dark red. Once the flowers have withered and fallen the plants display the green pods which are the cotton bolls. Inside the boll, seeds form and the cotton fibres grow and expand until the boll splits and the cotton becomes visible, like cotton candy balls perched on the plant's branches.
Picking
Cotton-picking machines twist the cotton balls from the branches and remove the seed before collecting the cotton into a basket. The cotton is then moved from the field to the gin building where the cotton is dried and cleaned. At the gin, seed and fibres are stored in dense bales and it is these that are sold to textile mills for manufacturing.
Spinning
These raw cotton bales arrive at the mills where they are cleaned further using a blowing and beating method. Short fibres can be separated for use in other industries, whereas the longer fibres are carded, a process that combs the raw material to remove natural build-up and to align the fibres so that they can be twisted into sliver. It is the sliver that is spun into yarn for the weaving or knitting of textiles.
Weaving
Looms work to weave the fabrics and textiles, interlacing yarns to form the warp and weft. It is here that the traditional bedding weaves of percale and sateen are woven and thread counts are chosen. These fabrics are known as ‘greige goods’ and they are sent to the finishing process or stored for future use.
Finishing
Taking the greige and finishing are the processes that make the textile fit for purpose. Finishing processes include singeing to remove fine hairs on the surface of the cloth; scouring to remove any leftover impurities; whitening to prepare the fabric for dyeing, and mercerizing, a process that ensures fabric shrinkage will be much lower for customers.
Following drying, fabrics may be treated with chemicals to change the behaviour of the fabric, these may include stain repellents, anti-allergen treatments or brightening agents.
Manufacturing
Finished cotton is then made into product for Vision, including flat and filled bedding items, towels, tablecloths and napkins to name a few.
Vision holds stock at griege stage to be able to manufacture and supply products according to demand and orders, as well as fully finished stocks to fill demand at short notice.
Vision is a proud member of Better Cotton and we source fully accountable cotton from around the globe. Find out more about how Vision sources cotton responsibly: https://corp.visionlinens.com/corporate-social-responsibility/
Looking to start your journey with Vision Linens? Join our loyalty club and start earning points.